工业4.0专业实验室解决方案
工业4.0是德国提出的一个高科技战略计划,是指以信息物理系统CPS(Cyber-PhysicalSystem)为基础,以生产中的供应、制造、信息高度数据化、网络化、智能化为标志,最后达到快速、有效的、智能的个性化产品供应。
本方案以工业自动化生产制造系统为设计蓝本,演绎现代工业控制中的各项基本技术的结合与应用;依据现有成熟技术、成熟装备进行技术集成,通过工业现场总线和计算机网络将各个硬件设备互相连通,在确保每个组成单元稳定可靠的基础上,有机的把各个单元组合、优化成具有一定创新性、先进性的符合工业4.0标准的数字化计算机集成制造系统。该系统适用于高等院校综合实训室建设需要,是一套有针对性的培养学生工业自动化与数控加工领域综合能力的实训系统。
一、智能制造实验室方案概述
智能制造实验室包含制造总控系统、执行系统、装配检测系统、生产信息系统,为一个自动化集成应用组合系统,它集成包含了原材料管理、数字化设计、加工、柔性化装配、混合输送、集中存储等一系列自动化过程,能充分展现在复合型生产中进行数字化管理生产的各个环节。
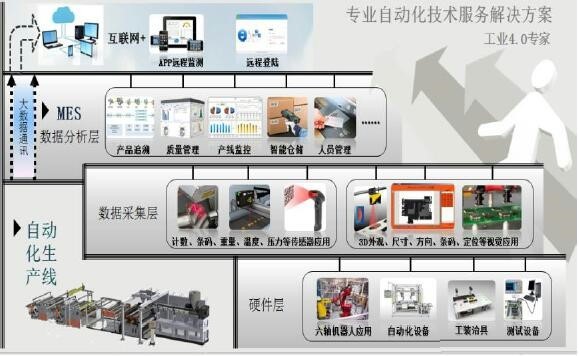
智能制造实验室系统包括:数字化设计、原材料/成品出、入库模块;加工模块;视觉检测模块;装配模块;激光雕刻模块等。依托于一条环形传输系统,可实现全自动化毛坯出库、车削加工、钻铣加工、雕刻加工、视觉检测、装配、成品入库、生产信息存储追踪等功能。
系统中各项内容具有高集成度、高度开放性、功能完善、先进、模块化和可扩充性等特点,在尽可能趋近工业化同时又立足于教学,充分考虑学员的参与性,做到教学与工业的无缝对接,使学员既可以系统的学习又可实际操作。
二、智能制造实验室系统组成
智能制造实验室系统由1个总控单元和多个从控单元(传输单元、仓储单元、加工单元、检测装配单元)组成;本产品采用模块化设计,即可单站控制,也可联机通讯;本系统依托于一条环形传输系统,完成了原料出库、车削加工、钻铣加工、视觉装配、成品入库等系统功能。
1、原材料出入库模块
该模块由货架、堆垛机、AGV小车等组成,通过无线通信网络从总控获取需要的原材料出货指令,将物料从立体仓库自动捡出。货位检测传感器采用无线通讯方式,并将结果反馈给总控,记录仓库出货信息。堆垛机采用X/Y轴采用同步带直线模组,采用伺服电机控制;Z轴采用双轴气缸与直线导轨配合,货叉形式。
2、加工模块
该模块主要由一台数控车床、一台钻铣床、一个6轴机器人,相应直线导轨组成,机器人负责机床的上、下料和原材料与半成品的搬运,加工完成的半成品被放置到传送带上。
3、装配模块
该模块负责将智能加工线输送来的半成品进行装配。产品装配是根据订单要求进行的。个性化的定制生产将在这个单元中实现。
4、智能视觉检测模块
该模块对装配后产品进行颜色、体积和加工缺陷进行检测,合格品及不合格产品将通过RFID读写器写入电子标签中,并最终被分别输送至仓库成品区和废品区,实现产品信息跟踪。
5、激光雕刻模块(仅在参观演示中使用)
对产品进行激光雕刻,可以雕刻手签名。
以上模块采用模块化设计,可独立运行也可与其它模块组合运行,体现工业4.0智能制造模块化、自适应的特点。
6、生产管理系统
生产管理系统的主要功能是通过该系统接受生产订单信息,可通过平板电脑下单,也可接受互联网智能终端传递的生产订单信息。
总控台电脑装有总控组态软件,可实时监控生产线各(不小于22寸);向各设备发送指令,控制各设备的运行、停止和等待;记录生产调度的历史信息;统计生产的产品数量类型;与客户端 互动,定时或按要求向客户端发送生产进度信息,使客户了解当前订单加工状态。
7、 控制系统
采用一网到底的实时工业以太网通信技术。实现智能工厂信息化、智能制造云端化。总控软件与各设备之间所有指令、信息按需要可以通过有线和无线网络两套系统进行连接。实现不同单元、不同功能模块或设备之间的数据信息互联、互通。
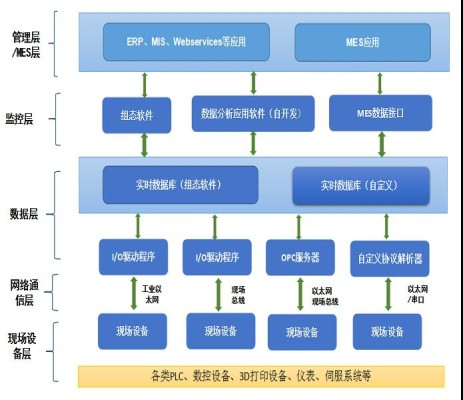
三、智能制造实验室系统工艺流程
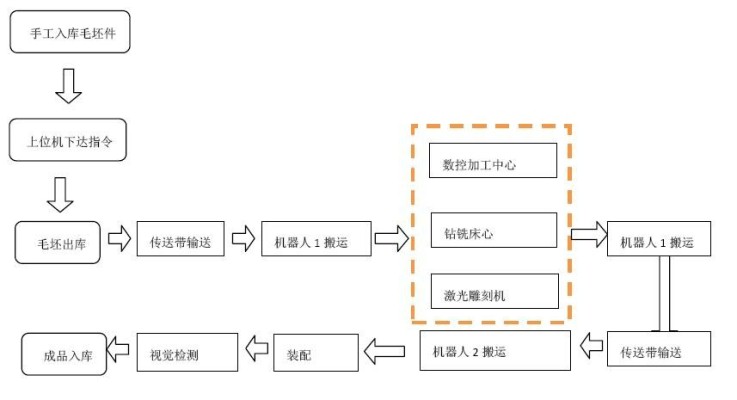
1、毛坯件由人工手动放入库位,毛坯托盘上装有RFID 载码体,通过手动录入记录毛坯的材质、颜色等相关信息;每个库位将放有固定的毛坯工件;
2、通过上位机下达生产任务或根据客户的定制任务,依据下达的加工件的工艺规划或加工要求选择加工设备;
3、每个加工设备毛坯件均存于立体仓库中,根据加工要求及数量进行毛坯件出库,毛坯件存放于托盘内;
4、收到出库指令后,由堆垛机进行毛坯件出库;堆垛机由XY三轴,XY轴联动,将货叉放入指定库位处,Z轴插入货叉,将工件及托盘提升,Z轴复位,托盘脱离仓库,XY轴联动,将工件及其托盘放置在立体仓库中转台上;
5、AGV小车接收到仓库中转台信号后,运行至中转台指定处,AGV小车平台上的输送机构工作,将物料自动接送至AGV小车输送平台;而后AGV小车沿指定线路行走至线体接料平台处,完成物料由AGV向线体传输的工作;
6、工件及其托盘放置于线体后,通过RFID读取毛坯件信息;
7、根据毛坯件信息选择不同加工设备,到达对应的加工设备后,线体挡停机构进行挡停;
8、在毛坯件信息读取后,工件到达加工设备前,机器人行走工作并到达指定加工设备定位点,等待完成工件从线体到加工设备之间的搬运、取放工作;
9、以此类推,机器人通过行走机构行走于各加工设备之间,负责不同工件在不同加工设备间的搬运取放工作;加工完成后由机器人分别放回线体托盘上各工件对应放置区域内;
10、待工件加工完成后,通过循环线体将工件运送至检测装配区域,并通过线体挡停机构进行挡停,同样由另外一台机器人实现工件在线体和检测装配工位之间的搬运工作。
11、工件装配后,线体托盘被送送至视觉检测设备上,按照进行工艺要求的进行形位公差检测,将检测不合格产品通过RFID标记;
12、入库前RFID读写头将检测信息、加工信息等写入对应工件托盘的RFID中,通过上位机进行工件信息、加工进度等显示;
13、到达入库定位点后,堆垛机工作,将工件装配体及其托盘放入指定库位,其流程与毛坯件出库相反;
14、每一个被设计加工部件,都拥有自己独立的ID身份,进行自记录,因此,整个系统将可以产生回溯的作用;从而使得未来的故障查找与诊断,具有高度智能的可回溯特征。
四、智能制造实验室系统适合开展的实训教学项目
(一)适合开展的实训内容
(1)机器人实操:机器人的硬件连接(本体、控制柜、示教器等);机器人的示教器调试与计算机调试;机器人的I/O通信(定义数字输入输出信号);I/O信号监控与操作;机器人的程序建立、编程;机器人以太网通信功能等;
(2)数控加工:数控系统调试;加工工艺设计;加工程序的编制;
(3)视觉引导:视觉检测与PLC之间通讯设置;配套视觉软件调试;
(4)射频识别:RFID与PLC通信设定;RFID配线、信号采集;
(5)编程控制:电气原理图、程序流程图的绘制;可编程控制器的编程与调试;编程软件的应用;
(6)通讯控制:以太网通讯控制;网络系统构成与拓扑图布局;PLC总/从站设定;PLC与RFID及机器人之间的通讯;PLC与人机界面之间变量通讯;
(7)电机驱动:伺服电机定位调速控制;三相减速电机的变频调速控制;
(8)传感检测:光电、电感、电容、霍尔等开关量传感器的安装、配线、信号采集与调试;
(9)机械装调:装配工具、测量工具、机械辅料的应用;直线模组、同步带轮、带支撑光轴、工装夹具等机械执行机构的识图安装与调试;
(10)气路搭建:气路图的识图与绘制,气路的搭建与阻挡气缸、三轴气缸、宽型气爪等气动执行元件的安装调试;
(11)低压配电:按钮、指示灯、断路器、继电器、塔灯等配线与调试;
(12)人机交互:人机组态的界面绘制与变量调试、组态软件的应用;
(13)识图配线:配线工具、配线辅料、线号标识的应用;信号线、电源线的导线对接。
(二)适合开展的实训项目
(1)西门子数控系统的设计与应用
(2)西门子数控系统组成实验
(3)西门子数控系统编程实验
(4)西门子数控车床电气控制系统设计实验
(5)西门子数控铣床电气控制系统设计实验
(6)西门子数控系统电气维修实验
(7)西门子PLC的编程与应用开发实验
(8)故障检测技术技能培训
五、智能制造实验室系统布局效果图
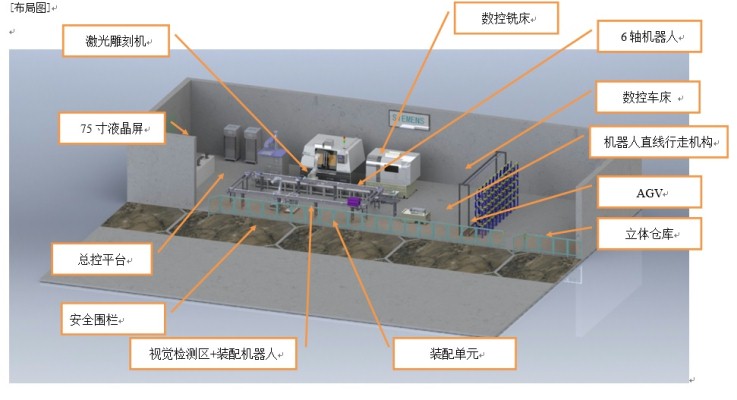